Anwendungsbeispiele für das Überwachungssystem WeldQAS in der industriellen Schweißfertigung

- Zwei Roboter, die an zwei Werkstücken jeweils dieselbe Naht schweißen sollen, wurden ungleich programmiert. Obwohl die Nähte äußerlich fast identisch sind, weisen sie verschiedene Einbrände auf.
- Unser WeldQAS - Überwachungssystem erkennt die ungleiche Einstellung der Roboter
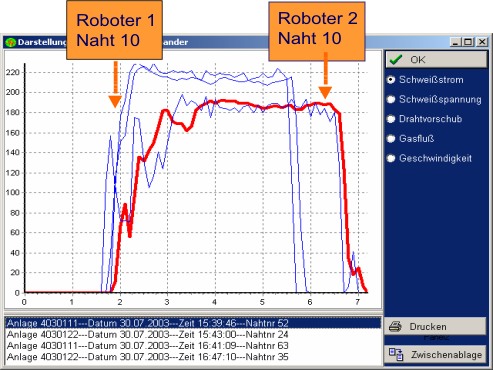
- Durch statistische Auswertungen können Schwankungen und Trends infolge von Chargenänderung, Verschleiß etc. erkannt werden.
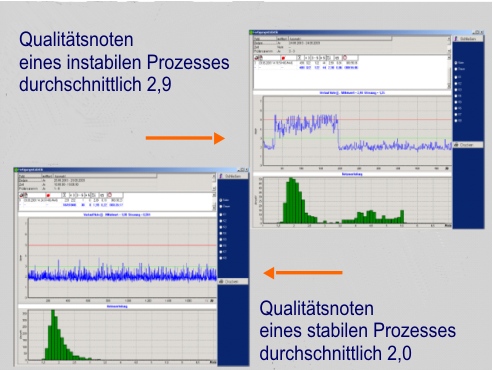
Ein Hersteller fertigt Turbinenwellen für große Wasser- und Gasturbinen (Länge 20m, Durchmesser 1,50 m) als auftragsbezogene Einzelstücke, die sehr hohen Belastungen widerstehen müssen.
Dabei kommt unter anderem das UP-Engspaltschweißen zum Einsatz. An das Resultat werden sehr hohe Anforderungen hinsichtlich der Einhaltung der Achssymmetrie und sehr kleiner Unwuchten gestellt.
Die Schweißnaht besteht aus einer Vielzahl von Lagen, die in einem durchgängigen Schweißprozess an großen automatisierten Anlagen erfolgt. Die Teile werden vor dem Schweißprozess vorgewärmt.

- Ein Schweißfehler, der erst in der Endkontrolle der Engspaltschweißnaht durch Ultraschallverfahren bemerkt wird, stellt somit bereits ein unlösbares Problem dar, da dieser bereits durch 20 Schweißlagen überdeckt sein kann. Durch den Einsatz der Schweißdatenüberwachung wird die Einhaltung der Schweißwerte und die Kontrolle des Lichtbogens während der bis zu 23 h dauernden Schweißung ständig vorgenommen.
- Durch die vielen Schweißlagen müssen eventuelle Probleme rechtzeitig erkannt werden, bevor weitere Schweißlagen die fehlerhafte Stelle überdecken. Im Unterschied zur Massenproduktion stellt die Turbinenwelle bereits in der Schweißfertigung einen erheblichen Wert dar. Allein die Vorfertigungsstufen nehmen teilweise mehrere Monate in Anspruch.
- Mittels einer berührungslosen Erfassung der Werkstücktemperatur wird die Einhaltung der zulässigen Vorwärm- bzw. Zwischenlagentemperaturbereiche überwacht.
- Durch die Schweißdatenüberwachung wird der Schweißer jederzeit über den Zustand der Schweißung informiert. Bei auftretenden Abweichungen entscheidet er darüber, ob er die Schweißung fortsetzt oder eine Nachbesserung einleitet.
- Neben der Überwachung wird der Schweißdatendokumentation eine große Bedeutung beigemessen, da die Fertigungsdaten von jeder Turbinenwelle und jedem Fertigungsschritt dokumentiert und 20 Jahre archiviert werden müssen.
- Die angefallenen Schweißdaten werden automatisch in das Datennetz des Betriebes übernommen.
- Die Dokumentation der Schweißnähte für jedes Teil ist bei dieser Art der Fertigung zu aufwendig und kann auch später nicht verwendet werden, da die Teile und die Ergebnisse nicht zugeordnet werden können.
- Die Auswertung von Fehlerprotokollen und statistischen Zusammenfassungen gibt dem Hersteller die Möglichkeit, die Anzahl der fehlerhaften Teile zu kontrollieren und rechtzeitig auf eine Erhöhung der durchschnittlichen Fehlerrate zu reagieren.
- Die Daten werden deshalb in einem Ringspeicher erfasst und nach Auswertung nur als Zusammenfassung gespeichert.
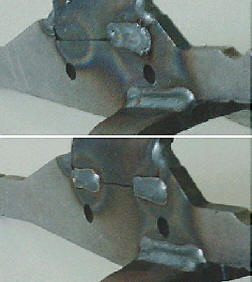
Ein PKW-Zulieferer unterhält eine Fertigung von Schalthebeln für PKW-Getriebe. Die Fertigung erfolgt dabei in Fertigungsstraßen, wobei der Schweißprozess der gestanzten Teile nur einen Fertigungsschritt darstellt. Die Fertigung ist hocheffektiv und nur auf wenige Typen ausgelegt. In einer Fertigungsstraße werden nur Teile für eine Sorte Schalthebel gefertigt. Am Ende der Fertigungsstraße erfolgt die direkte Ablage in die Auslieferungspaletten des Getriebeherstellers. In einer Minute werden dabei 6 Schalthebel in einem Schweißautomaten gefertigt, wobei jedes Teil gleichzeitig von 6 Schweißbrennern bearbeitet wird. An einem typischen Arbeitstag werden bis zu 5400 Teile hergestellt und dabei 32400 Schweißnähte mit einer Dauer von 2 bis 6 s geschweißt. Die Anforderungen an die Schweißnähte sind nicht kritisch, aber alle Nähte müssen diese Anforderungen bei jedem Teil erfüllen.
Die Anlage ist so ausgelegt, das fehlerhafte Teile automatisch aussortiert werden.
Unsere Aufgabe:
Nachweis der Erkennung von sichtbaren Schweißunregelmäßigkeiten beim MAG-Schweißen.
Der Kunde wünschte eine einfachere und robustere Handhabung als bei der vorhandenen optischen Nahtvermessung (nach dem Schweißen) sowie Nachweis einer sicheren Durchbranderkennung.
ThermoProfilScanner
Nachlauf zum Brenner: 40 mm
Abtastfrequenz: 100 Hz
Auflösung: 0,9 mm
Arbeitsabstand: 60 mm
Gasspülung Schutzgas: 3 l/min
Schweißgeschwindigkeit: 60 cm/min
Keine Wasserkühlung
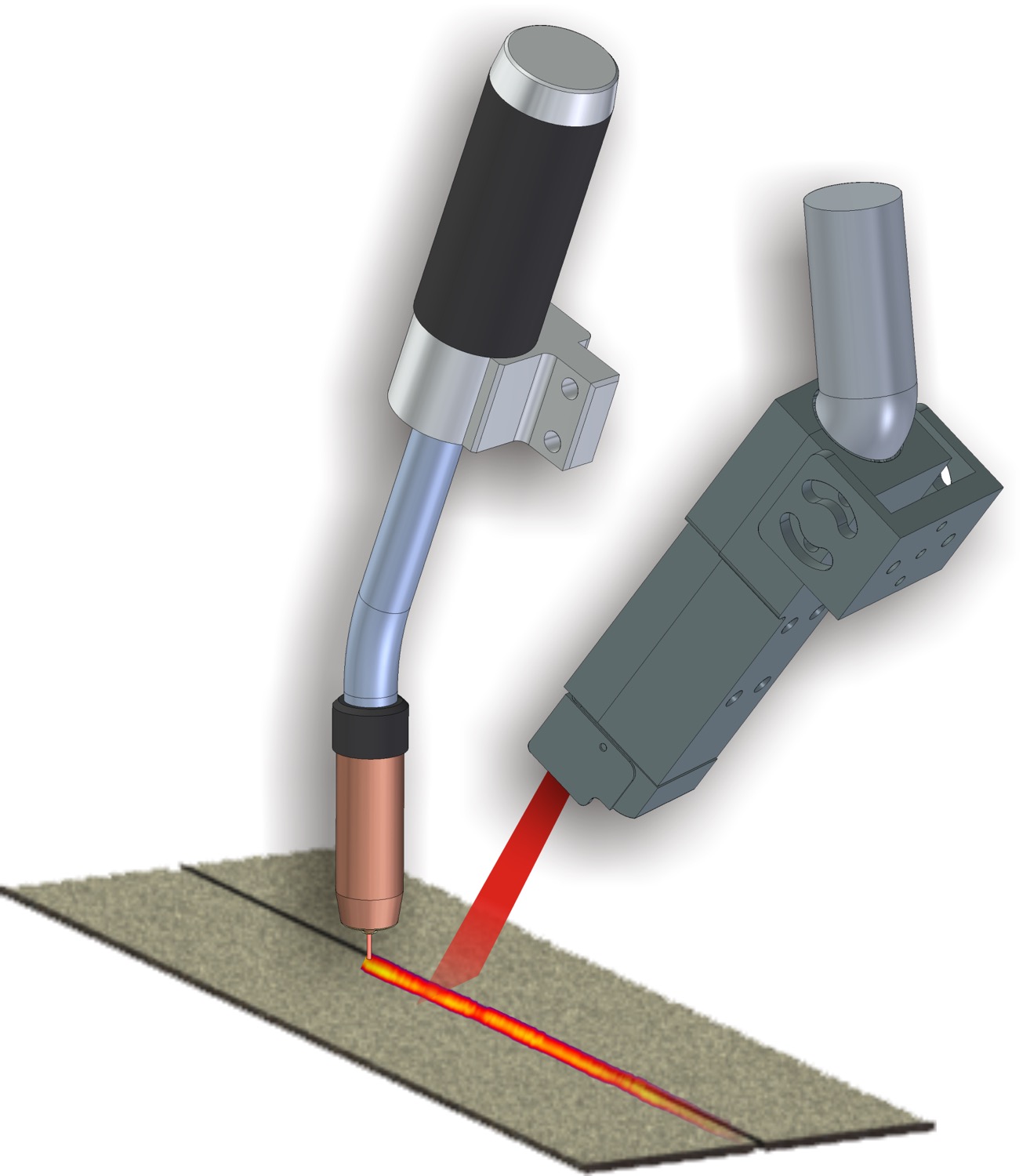
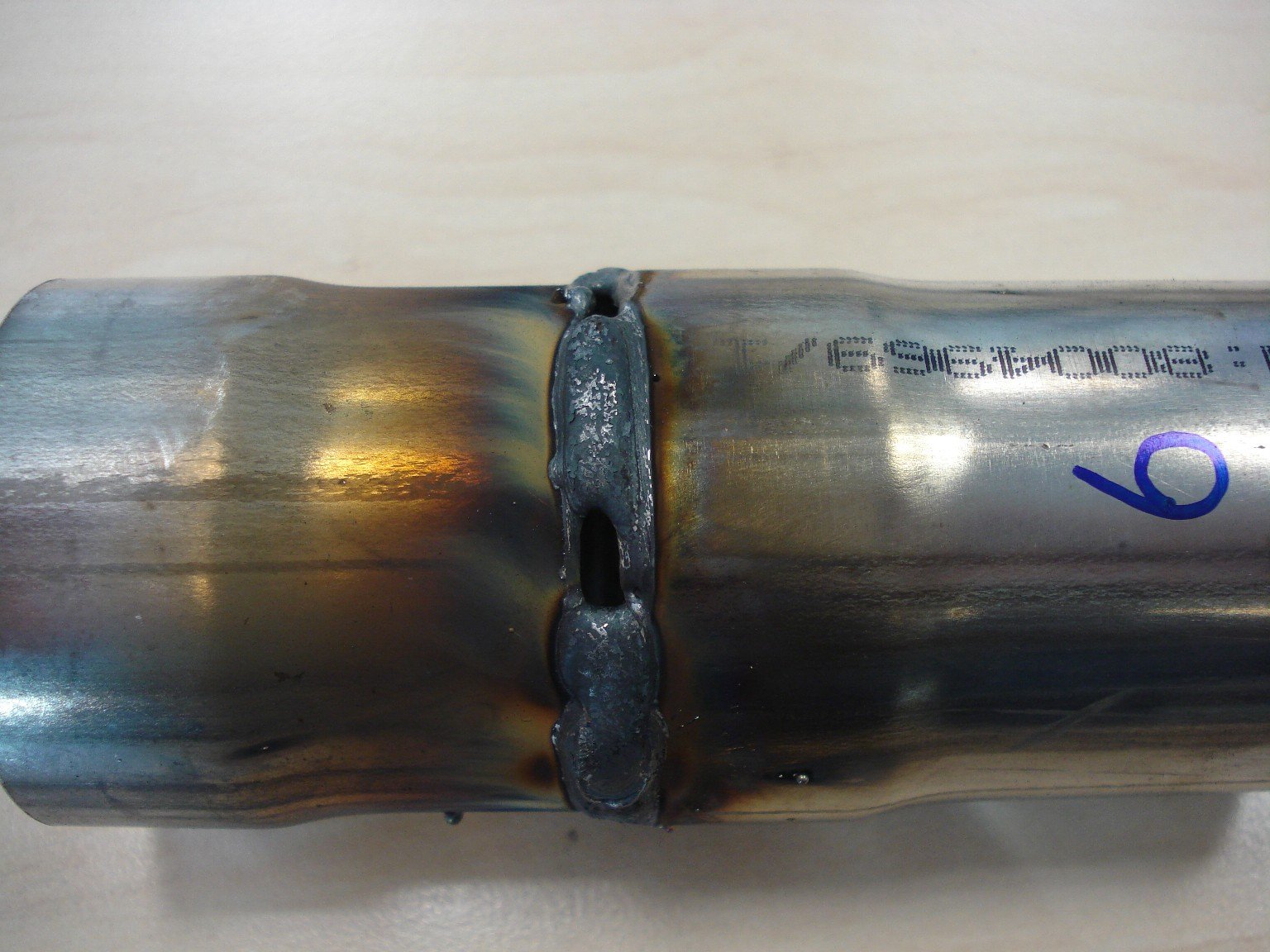
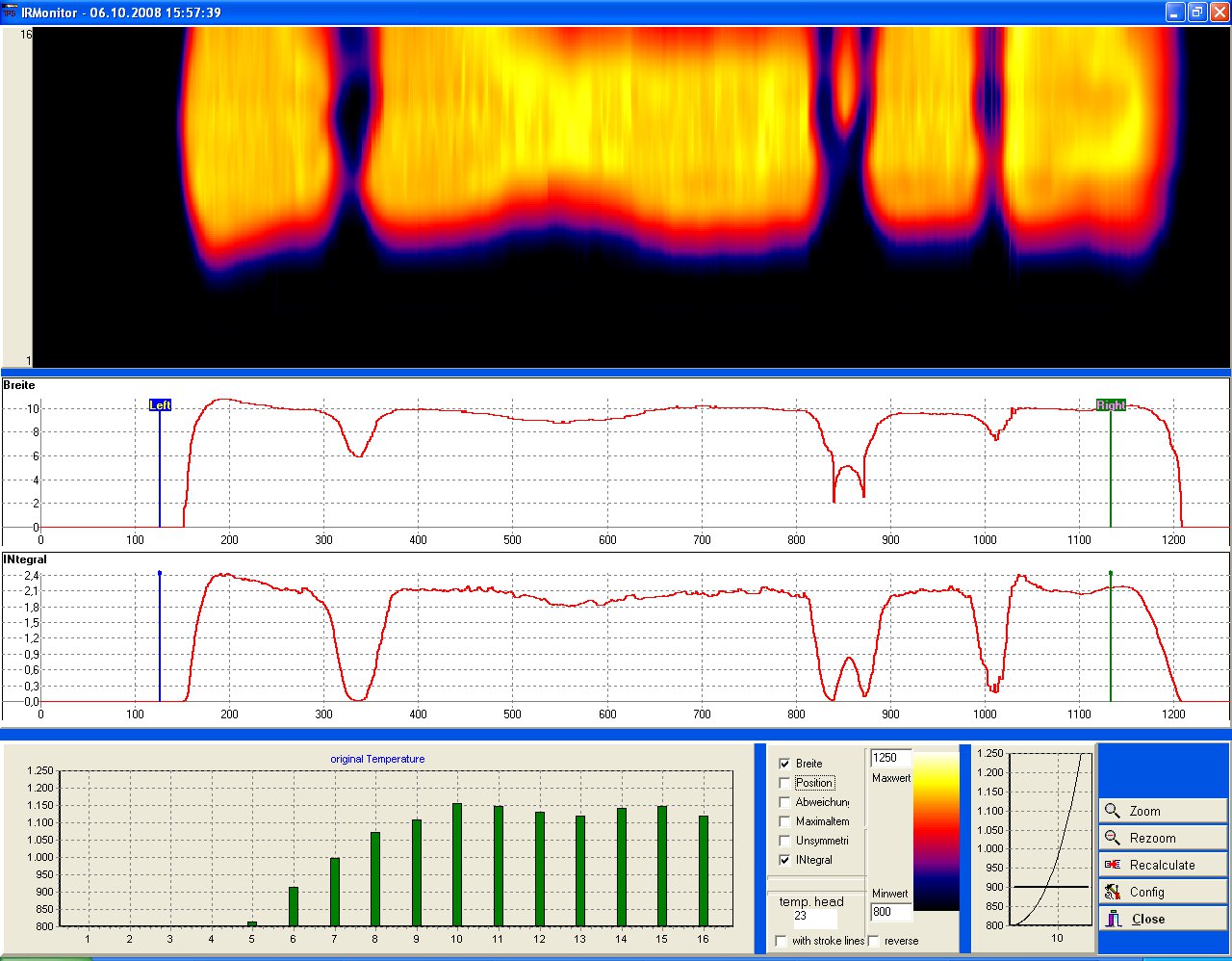
Fehlerbild: mehrfache Durchbrandfehler
Durch die schlechte Wärmeleitung des Cr-Ni-Werkstoffes erfolgt der Durchbrand erst ca. 15 mm nach dem Lichtbogen. In diesem Fall sind in Schweißstrom und Schweißspannung keine Durchbrandmerkmale erkennbar. Daher ist dies eine typische Anwendung für den TPS.
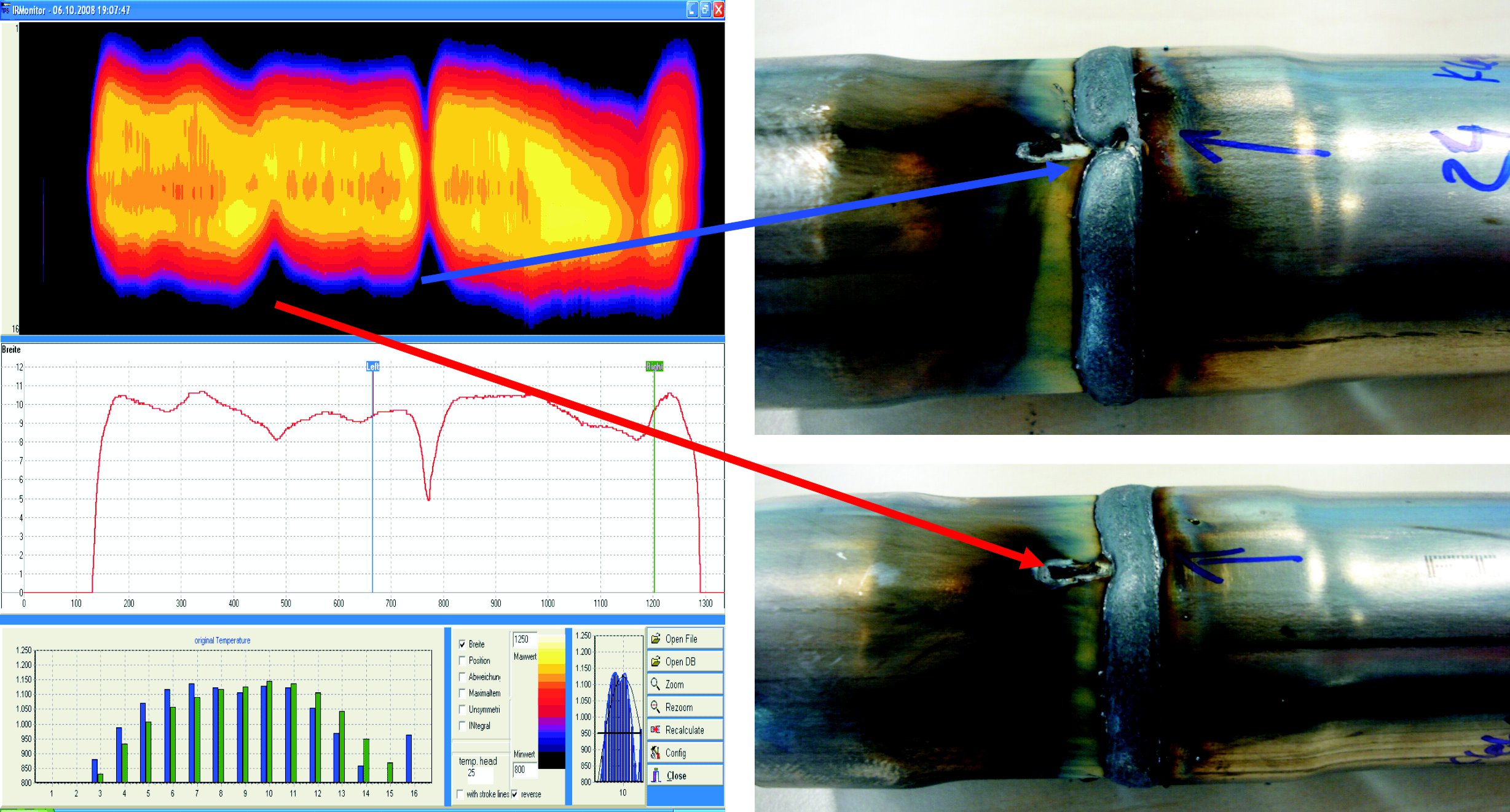
Fehlerbild: geometrische Abweichungen und Nahteinschnürungen von 0,8 – 2 mm
Unsere Aufgabe
Erkennung von sichtbaren Schweißunregelmäßigkeiten
wie Bindefehlern und Poren größer 1 mm.
ThermoProfilScanner
Nachlauf zum Brenner: 7 mm
Abtastfrequenz: 100 Hz
Auflösung: 0,9 mm
Arbeitsabstand: 130 mm
Gasspülung Schutzgas: 3 l/min
Schweißgeschwindigkeit: bis zu 3 m/min
Keine Wasserkühlung
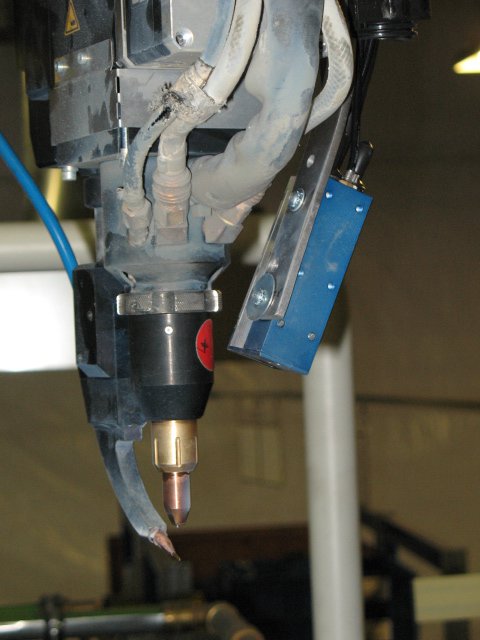

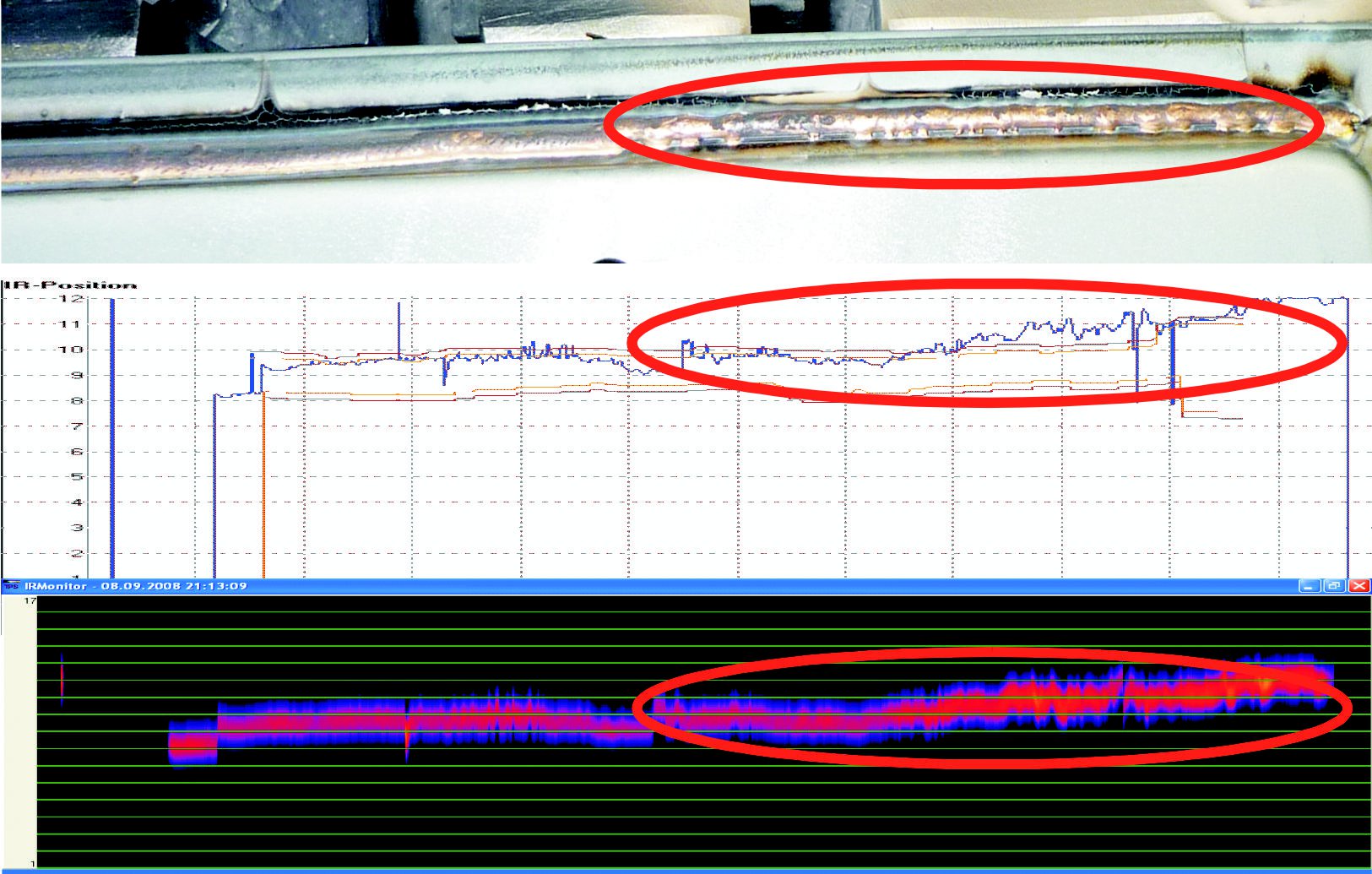
Die unmittelbare Fehlererkennung verhindert eine Weiterverarbeitung des Teiles bis zur Gesamtkarosse und spart damit 1000 EUR je rechtzeitig gefundenem Fehler.
Fehlerbild: großer Bindefehler
Bereits am Anfang verlagert sich die Naht an den Rand, dann Aufbruch und Bindefehler.
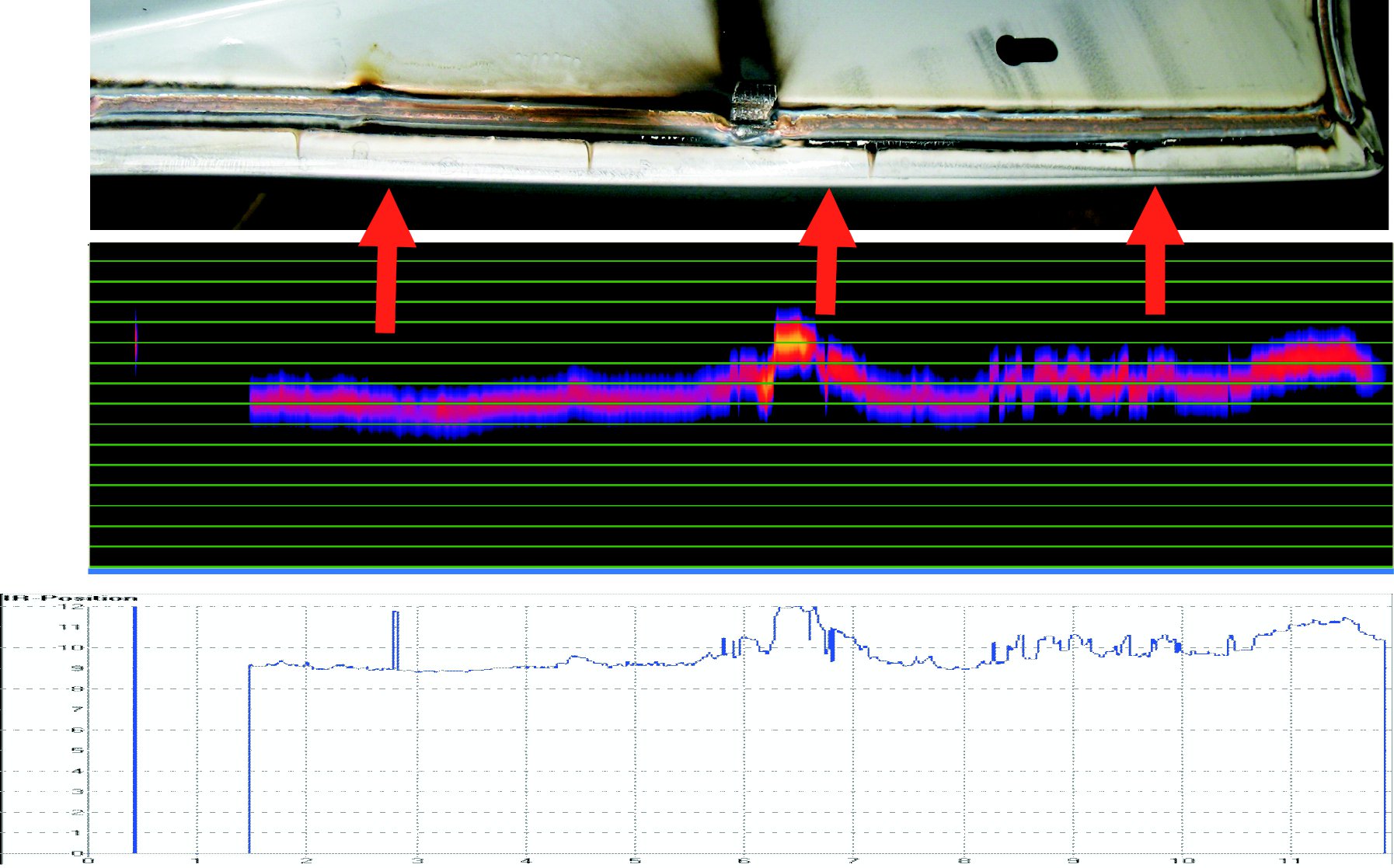
Fehlerbild: kleine Bindefehler
Bindefehler wurde verursacht durch schadhafte Elektrode
- Zunehmend unruhiger Nahtverlauf zum Ende der Lötung
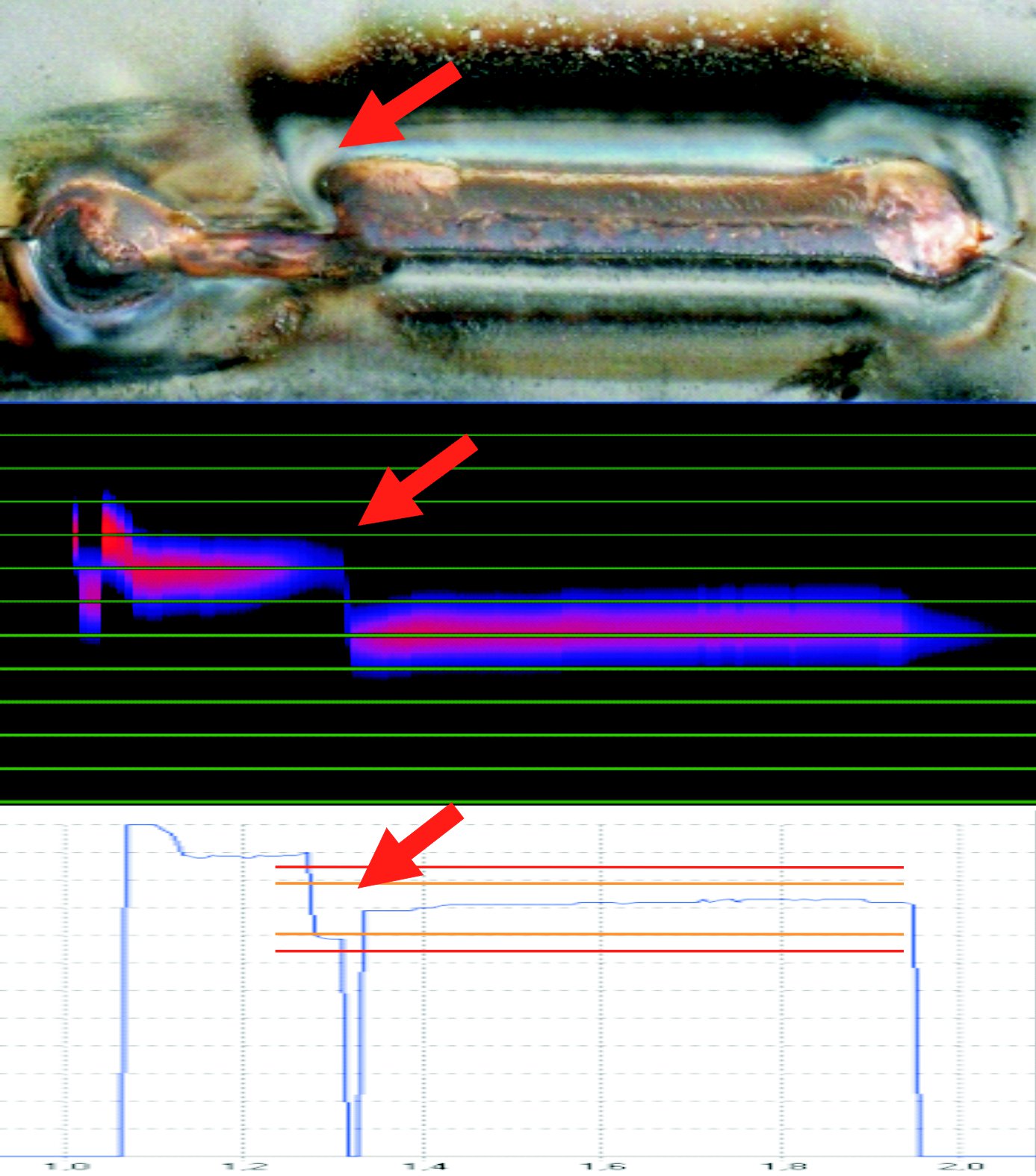
Fehlerbild: Keine Anbindung auf den ersten 5 mm