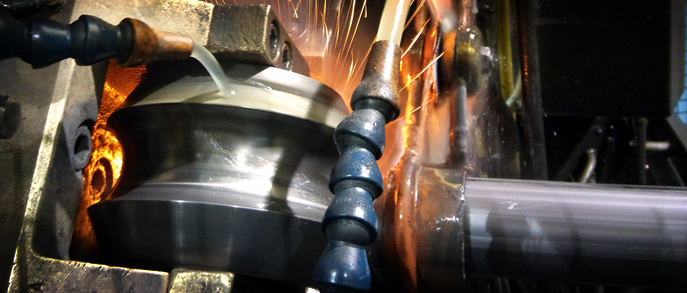
Den üblicherweise eingesetzten zerstörungsfreien Prüfverfahren zur Schweißnahtkontrolle wie Wirbelstromprüfung und Ultraschallprüfung sind insbesondere bei kalten Fügestellen (Klebenähten) Grenzen gesetzt.
Mit Anwendung einer neu entwickelten Wärmefelderfassung, dem Thermoprofilscanner, können diese und alle anderen Schweißunregelmäßigkeiten auch bei Schweißgeschwindigkeiten von 180 m/min sicher erkannt werden.
Gleichzeitig ermöglicht die Visualisierung und Parametrisierung des Wärmefeldes eine Prozessführung der Schweißanlage für eine genaue und reproduzierbare Schweißnahtqualität.
Beim Schweißen werden durch örtlichen Energieeintrag Werkstoffe geschmolzen und im Gefüge gewandelt.
Die korrekte Wärmeeinbringung als auch die ungestörte Wärmeausbreitung sind ein entscheidendes Merkmal zur Beurteilung der Schweißnähte.
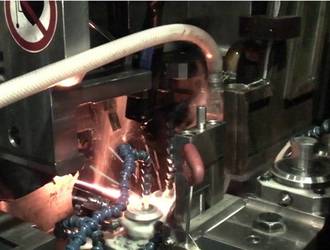
Das menschliche Auge kann Wärmestrahlung nicht erfassen. Der sichtbare Teil der glühenden Naht überstrahlt die Wärmeinformationen um ein Vielfaches.
Dazu ist eine Technik nötig, die diese Wärmeinformationen dauerhaft, hoch genau und unter den Bedingungen der Produktion reproduzierbar messen kann. Für diese Zwecke und den Erfahrungen aus 19 Jahren Schweißfertigungsüberwachung wurde der ThermoProfilScanner entwickelt und patentiert.
Weitere Informationen finden sie in unserer Präsentation TPS-3-Rohr-HFI
Messung des Wärmefeldes
Übertragung der Wärmeprofile an das Überwachungssystem WeldQAS, hier erfolgen Darstellung, Überwachung, Speicherung und Auswertung.
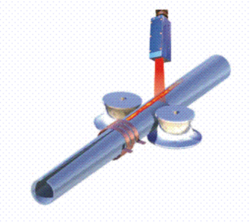
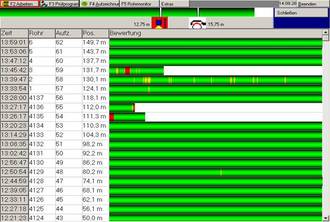
Rohrmonitor
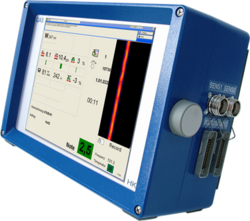
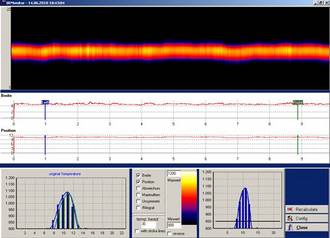
Wärmefeldauswertung
Aufgabe
- Schaffung einer Einstellhilfe für optimale Schweißparameter auf Basis des Wärmefeldes
- Erkennung von sichtbaren und nicht sichtbaren Schweißfehlern, kalte Fügestellen (Klebenähte), zu großer Wurzeldurchhang
- Farbmarkierung der Fehlerstellen
- Ablösung von Wirbelstromsystemen, die diese Fehler nicht finden können
Anwendungsdaten TPS
Nachlauf zum Schweißpunkt: 100 mm
Arbeitsabstand: 60 mm
Gasspülung Schutzgas: 3 l/min
Schweißgeschwindigkeit: 80 m/min
Wasserkühlung
Rohrmaß: 13 x 2,5 mm
HFI-Generator 250 kW – konduktives HF-Schweißen
Rohre werden auf Coil gewickelt
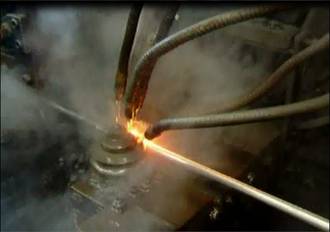
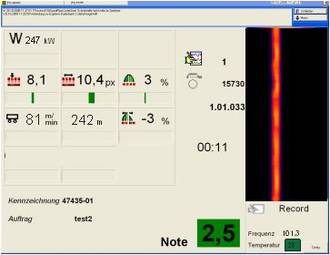
Arbeitsmonitor mit aktueller Nahtbewertung und Wärmefeld
Erfasst werden
- Generatorleistung
- Bandposition und -geschwindigkeit
Wärmefeld eines 21 m langen Rohrabschnittes
Aus dem Wärmefeld werden berechnet:
- Schweißnahtposition
- Breite der Temperaturzone
- Symmetrie des Wärmefeldes
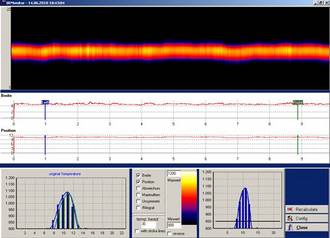
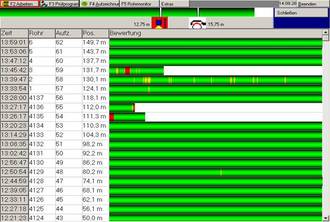
Besonderheiten beim Endlosrohrschweißen
Rohr-Monitor - Grafische Darstellung der letzten 40 Rohre
Wärmefeld bei Fehler durch kalte Nahtstelle
Wird die Schmelztemperatur nicht mehr erreicht, sinkt die Temperatur in der Fügezone.
Der Sensor ermittelt die Breite des Wärmefeldes über einer festgelegten Temperaturschwelle. Zu kalte Schweißnähte (Klebefügung) zeigen sich sehr deutlich in der abnehmenden Wärmefeldbreite.
Auffinden von kalten Fügestellen
Breite des Wärmefeldes mit eingelernten Grenzwerten.
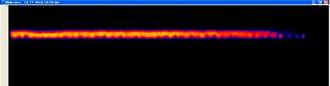
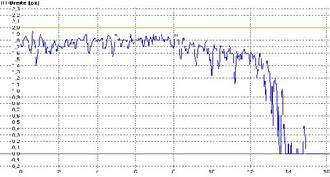

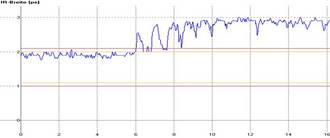
Falsch eingestellte Schweißleistung
Wärmefeld bei zu hoch eingestellter Leistung
Infolge dessen entstehen Fehler wie zu großer Wurzeldurchhang, Spritzer, Verbrennungen.
Die Breite des Wärmefeldes zeigt den zu großen Wärmeeintrag.
Vergleichende Darstellung
Temperaturbild einer i.O. - Schweißnaht im Vergleich zu einer Naht mit ungleichmäßigem Wärmebild.
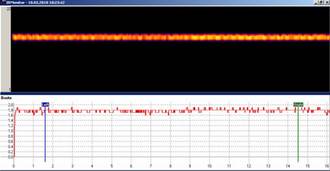
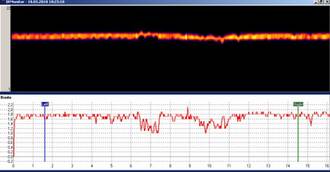
Aufgabe
Finden von kalten Fügestellen, (Klebenähte), die durch die integrierte Wirbelstrom- und Ultraschallmessung nicht erkannt werden.
Bisher war nur eine zerstörende stichpunktartige Prüfung möglich. Rohre, die unter Belastung beim Kunden undicht wurden, konnten bisher nicht aussortiert werden.
Sicherung einer konstanten Fertigungsqualität auf Basis des Wärmefeldes
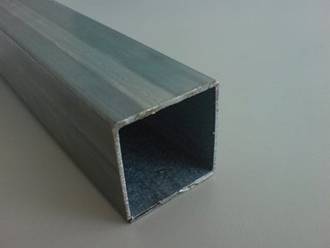
Anwendungsdaten TPS
Nachlauf zu den Rollen: 50 mm
Abtastfrequenz: 200 Hz
Arbeitsabstand: 120 mm
Gasspülung Schutzgas: 15 l/min
Schweißgeschwindigkeit bis zu 60 m/min
Wasserkühlung
Fehler in der Leistungsanpassung
Stahl - Rohr 13*2,2 mm, 5,6 m lang
(rote Markierung)
Bei zu hoher Energie kommt es zu einer sehr starken Aufheizung
(hier für die Dauer von 0,85s.
Die Temperaturen sind höher und die Wärmezone ist deutlich breiter.
(blaue Markierung)
kalte Fügestelle (0,3s lang)
Diese fehlerhaften Abschnitte werden mittels TPS und der dazugehörigen Überwachung sicher erkannt und markiert.
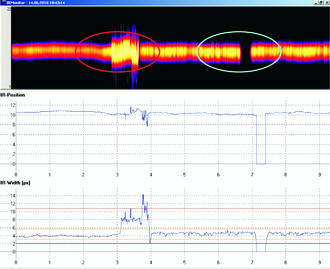
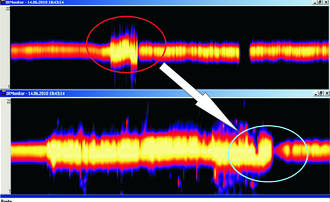
Beispiel für Sensibilität der Wärmerfassung an der Schweißnaht
Der gezoomte Bereichzu hoher Energie enthält am Ende eine kalte Stelle.
(blaue Markierung)
Kalte Stelle (Energieeinbruch) für die Dauer von 40 ms.
Diese fehlerhaften Abschnitte werden mittels TPS und der dazugehörigen Überwachung sicher erkannt und markiert.
Gegenüberstellung von Bandqualitäten
Stahl - Rohr 13*2,2 mm
Gleichmäßiges Wärmefeld (oben)
Ungleichförmiges Wärmefeld durch Schwankungen im Bandmaterial (unten)
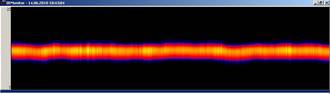
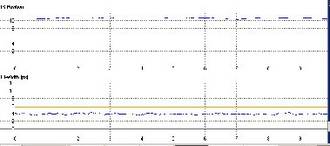
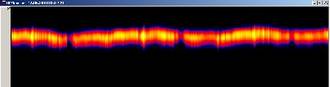
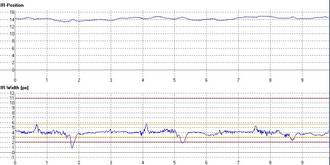
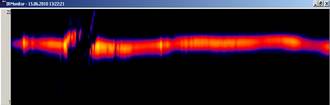
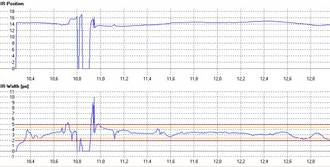
Wärmefeld beim Aufplatzen an der Nahtstelle zweier Coils
Stahl - Rohr 13*2,2 mm
Aufgabe
Erkennung von sichtbaren und nicht sichtbaren Schweißunregelmäßigkeiten wie Poren, Flankenbindefehler, unsymmetrischer Einbrand, ungenügende Wurzeldurchschweißung und Brennerfehlstellungen.
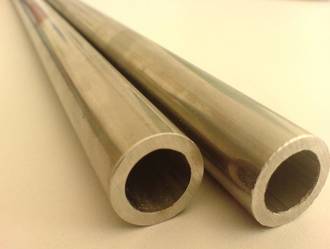
Anwendungsdaten TPS
Nachlauf zum Brenner: 20 mm
Abtastfrequenz: 100 Hz
Auflösung: 0,9 mm
Arbeitsabstand: 80 mm
Gasspülung Schutzgas: 3 l/min
Schweißgeschwindigkeit bis zu 1,5 m/min
Wasserkühlung
Fehlerbild: Falsche Brennerposition
Versatz des Brenners quer zum Rohr (Nahtsymmetrie)
CrNi - Rohr 20*3 mm
Eine nicht mittige Brenner-Position führt zu einem unsymmetrischen Einbrand. Eine Flanke wird stärker aufgeschmolzen als die andere.
Optisch kaum zu erkennen, aber Im Wärmebild des TPS deutlich sichtbar.
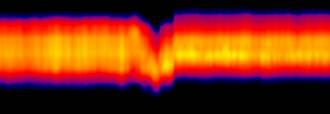
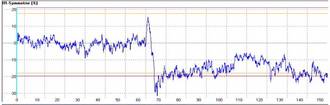
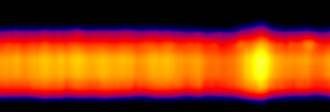
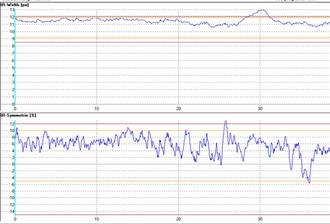
Fehlerbild: Poren
CrNi - Rohr 20*3 mm
Heißrisse und Poren stellen sich durch die gestörte Wärmeleitung im Wärmebild als „Hotspots“ dar. Diese Rohre sind nicht mehr gebrauchsfähig.
Fehlerbild: unsymmetrischer Einbrand durch versetzten Bandeinlauf
CrNi - Rohr 20*3 mm
Optisch nicht auszumachen, kommt es hier zur immer größer werdenden Unsymmetrie des Thermoprofils durch Verschleiß oder fehlende Schmierung des Rollensatzes.
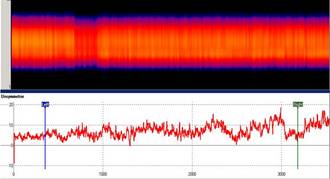
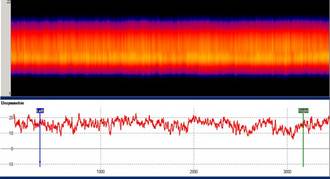
Aufgabe
- Überwachung und Darstellung des Einbrandes bei der Herstellung von nachträglich umgeformten, komplett geschlossenenem Schweißdraht
- Referenz: Anlagenbauer Bühler Würz Kaltwalztechnik GmbH, Pforzheim
- Rohr: 12* 2mm gefüllt mit Pulver
Schweißgeschwindigkeit 15 m/min
Das WeldQAS-System berechnet für jedes Profil (200 mal pro Sekunde) Merkmale des Wärmefeldes, die als Überwachungswerte Verwendung finden und besonders den Einbrand kontrollieren.
Es ist in der Lage, neben den Wärmefeldern weitere Parameter der Anlage, z.B. Laserleistung und Geschwindigkeit abzugreifen, synchron aufzunehmen und zu überwachen.
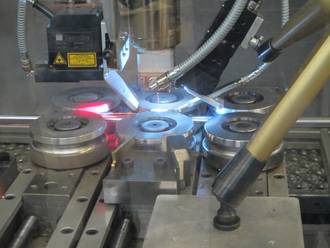
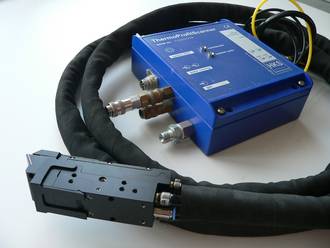
Anwendungsdaten TPS
- Wasserkühlung integriert
- Antispritzerschild
- mechanische Selbstschutzklappe
- Temperaturregelung der Aufnahmeelektronik
Einbrandkontrolle
Beispiel:
Lasereinkopplung wie vorgesehen, Einbrand gleichmäßig und bis zu 90 % der Naht
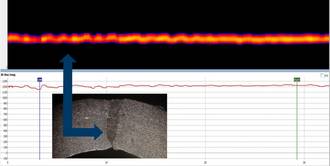
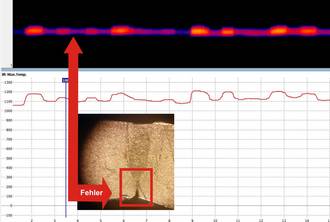
Einbrandkontrolle bei Abweichung der Laserleistung
Beispiel:
Gleichmäßiger, aber zu geringer Einbrand, weniger als 80 %
Einbrandkontrolle bei Lageabweichungen
Beispiel:
Bereits Abweichungen des Lasers von 0.05 mm über der 0-Fuge sind deutlich als unsymmetrischer Einbrand feststellbar.
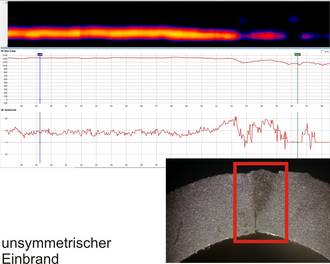
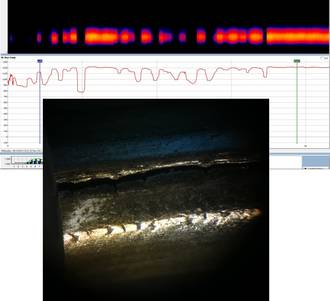
Einbrandkontrolle bei geöffnetem Spalt
Beispiel:
Entsteht ein kleiner Spalt in der Fuge kann der Laser seine Energie nicht in die Fuge einbringen. Der Einbrand ist nicht ausreichend.
Aufgabe
Erkennung von sichtbaren und nicht sichtbaren Schweißunregelmäßigkeitenwie Löcher, Poren größer 1 mm, Flankenbindefehler und Einbrandschwankungen.
Erkennung von Schweißbarkeitsproblemen im Zuliefermaterial.
Das eingesetzte Wirbelstromprüfgerät war für diese Aufgabenstellung ungeeignet.
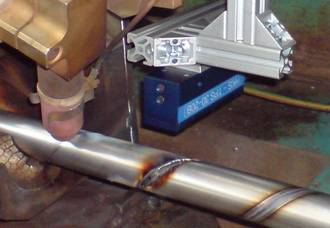
Anwendungsdaten TPS
Nachlauf zum Brenner: 40 mm
Abtastfrequenz: 100 Hz
Auflösung: 0,9 mm
Arbeitsabstand: 20-60 mm
Gasspülung Schutzgas: 3 l/min
Schweißgeschwindigkeit bis zu 3,5 m/min
Wasserkühlung durch Stromquelle
Arbeitsmonitor mit aktueller Nahtbewertung und Wärmefeld
Erfasst werden
- Schweißstrom,
- Schweißspannung,
- Schutzgasmenge,
- Bandposition und -geschwindigkeit
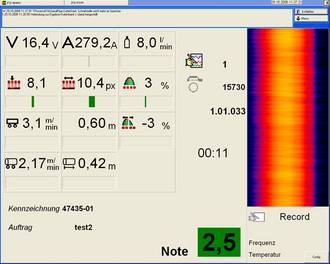

Wärmefeld eines 6 m Rohres
Aus dem Wärmefeld werden berechnet:
- Schweißnahtposition
- Breite der Temperaturzone
- Symmetrie des Wärmefeldes
- Maximaltemperatur
Fehlerbild: Durchbrand
CrNi – Band 73*1,0 Rohr 32mm
- Durchbrand erzeugt Wärmestau
- Ein Scann entspricht hier einer Abtastbreite von 0,62 mm.
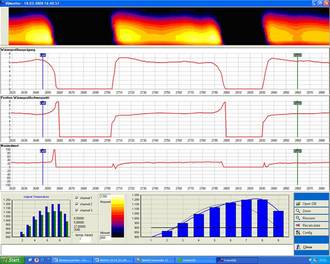
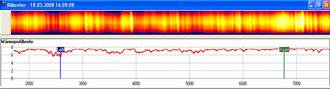
Fehlerbild:
ungleichmäßige Wärmeeinbringung
Stahlband 86*1,5 – Rohr 38 mm
Ungleichmäßige Wärmeeinbringung und Einbrandschwankungen durch fehlerhaftes Bandmaterial.
(äußere Merkmale – leichte fischgrätenähnliche Schuppung)
Fehlerbild:
Nahtversatz / Nahtlage
CrNi - Band 73*1,0 Rohr 32mm
Derartige Nahtversätze führen hier bei späterer Druckbelastung des Rohres zum Versagen der Schweißnaht.
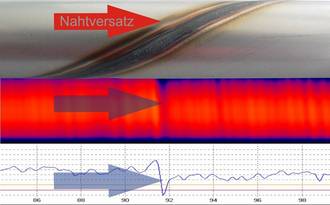