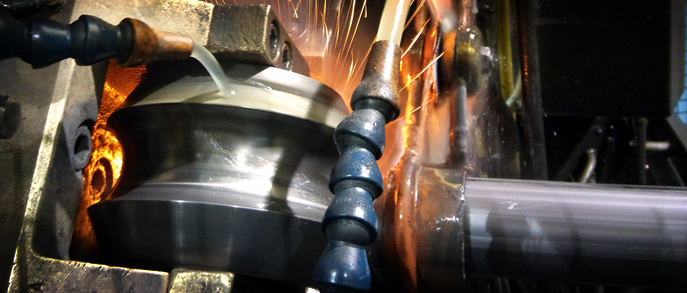
The usually used nondestructive testing methods for welded seam control as eddy current examination and ultrasonic examination fails at cold fusion points (bond seams).
with the newly developed measuring of the heat field via ThermoProfileScanner, these and all other welding irregularities can also be recognized at welding speeds up to 180 m/min.
The visualization and parameterization of the heat field enabled a process control of the welding plant for an exact and reproducible welded seam quality
While welding materials they are melted by a local application of energy and are changed in the structure.
The correct heat input as well as the undisturbed heat propagation are essential characteristics to judge the welded seams.
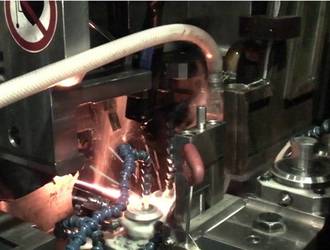
The human eye cannot register thermal radiation. The visible part of the glowing seam outshines the warmth information completely.
Therefore a technique is necessary, which can measure this temperature information durably, highly precise and reproducible under production conditions (pollution, smoke..).
The same temperature field guaranteed the same welding quality. For that reason and with 18 years experience the TPS was developed and patented.
measurement of the thermal field
System of welding data monitoring
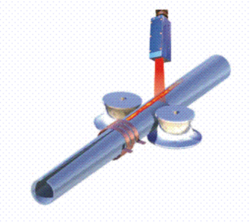
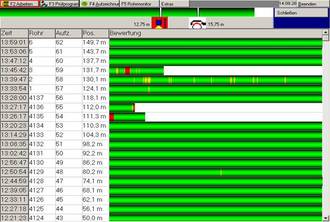
„tube“ - monitor
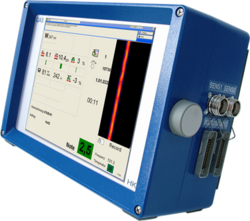
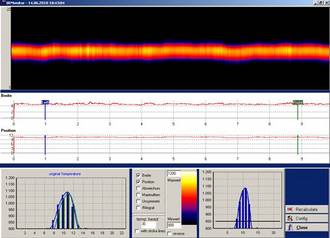
Analysis of the heat field
Task
- Realizing a set up help for optimal welding parameters based on the heat signature
- Recogognition of visible and invisible welding faults, cold joints, and excessive root penetration.
- Color marking faults
- Re-place Eddy Current Detection Systems since these can not detect these faults
Application Data TPS
Distance to torch : 100 mm
Working distance: 60 mm
Gas purge Shield gas: 3 l/min
Welding speed: 80 m/min
Water cooling
Pipe dimensions:13 x 2,5 mm
HFI-Generator 250 kW – conductive HF-welding
Pipes are spooled to coil
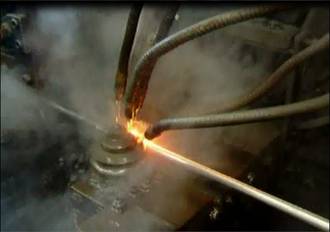
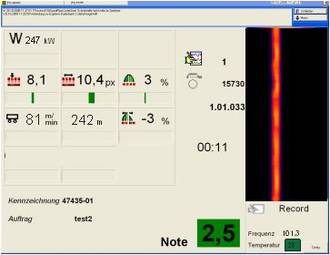
Work monitor with actual seam evaluation and heat signature
Captured are:
- Generator output
- Band position and -speed
Heat signature of a 21 m tube
Using the thermal field are calculated:
- Welding seam position
- Width of temperature zone
- Symmetry of heat field
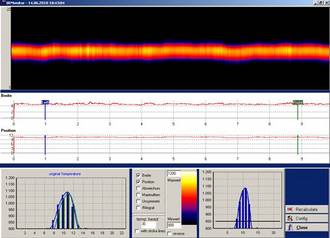
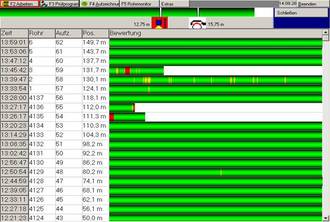
Special features for seam pipe welding
Graphic display of the last 25 tubes in tube monitor application.
Heat field when fault through cold fusion joint
When the melting temperature is not reached, the temperature is falling in the joining zones.
The sensor is calculating the heat field width via a set temperature threshold. Cold welding joints can be clearly seen in the diminishing heat field width.
Detecting cold fusion points
Width of heat filed and learned thresholds values.
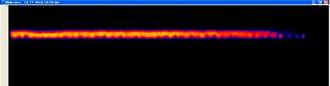
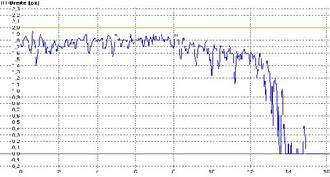

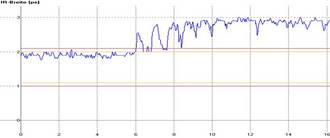
Welding capacity adjusted wrongly
Thermal field at too highly adjusted welding capacity
A result of that are failures like big excess penetrations, spatters, burnings.The breadth of the thermal field shows the heat input is too big.
Comparative representation
Thermal field of an i.O. - seam compared to a seam with irregular thermal field.
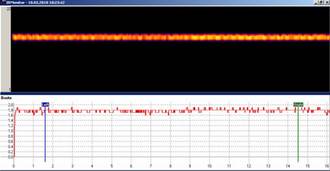
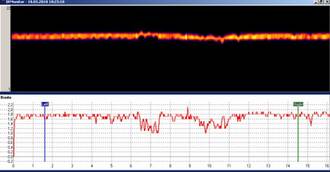
Tasks
- Detection of cold fusion points , (bond seams), which the integrated eddy current system and ultrasonic system could not recognize.
- Up till now only a destroying punctual testing of materials was possible. Pipes which got leaky later at the costumer could not be sorted out.
- Warranty of a constant quality based on the thermal field
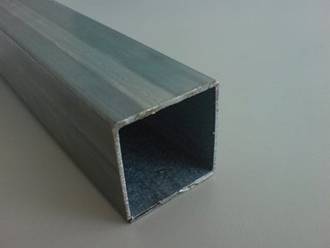
Application Data TPS
Distance to torch : 50 mm
Sampling rate: 200 Hz
Working distance: : 120 mm
Gas purge shield gas : 15 l/min
Welding speed up to 60 m/min
Water cooling
Failure in the adaption of energy power
steel - tube 13*2,2 mm, 5,6 m length
(red mark)
to high energy caused a very strong on-heating (for the duration of 0,85 s. The temperatures are higher and the heat field is considerably expanded (further zoom next page).
(blue mark)
cold fusion points (0,3s long)
These faulty sections are recognized and marked by the TPS and the additional monitoring system.
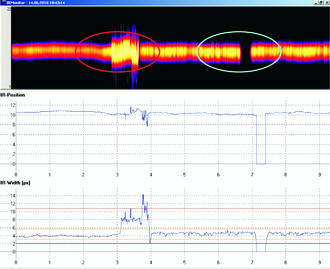
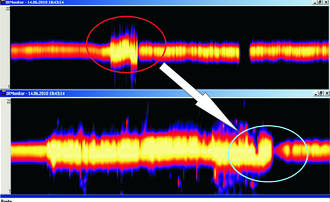
Example for the sensibility of the thermal measuring at the seam
(Red mark)
The area zoomed with to high energy (from previous foil) has a cold point at the end.
(blue mark)
Cold point (energy fall-off) for the duration of 40 ms .These faulty sections are recognized and marked by the TPS and the additional monitoring system.
Comparison of band qualities
steel - tube 13*2,2 mm
Regular thermal field
Irregular thermal field because of up- and downturns (fluctuations?) of the band material
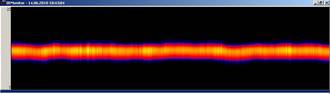
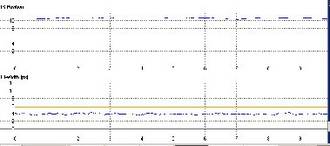
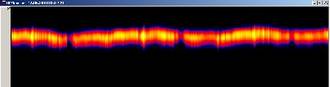
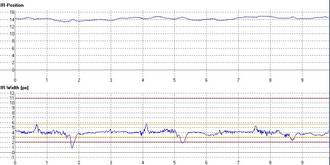
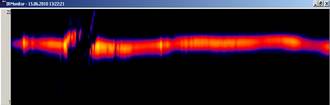
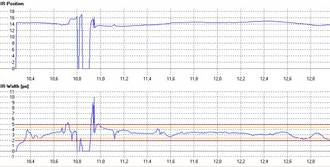
Thermal field while burst open at the junction of two coils
steel - tube 13*2,2 mm
Task
Detection of visible and invisible welding irregularities as pores, insufficient side-fusion, defect root penetration and the detection of torch misalignments.
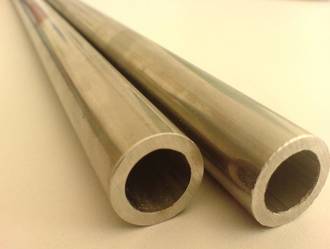
ThermoProfilScanner
offset to the torch: 20 mm
scan frequency: 100 Hz
resolution: 0,9 mm
working distance: 80 mm
purging gas: 3 l/min
welding speed up to 1,5 m/min
water cooling
Fault image: Torch is not in center line of the welding joint. (Seam symmetry)
CrNi - pipe 20*3 mm
An off- center torch position is causing an asymmetric penetration. One fusion edge is melted more than another.Optical hardly visible, but clearly visible in the heat signature.
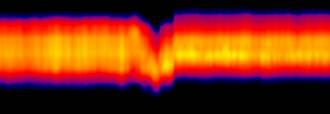
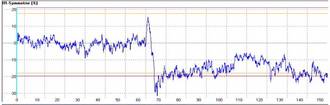
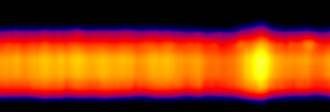
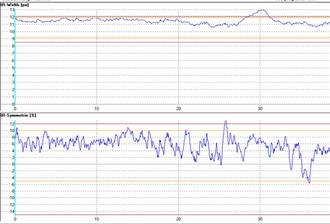
Fault image: pores
CrNi - tube 20*3 mm
Hot cracks and pores are represented as „Hotspots“ in the heat image. Faults like these are causing a disturbance in the heat conduction and are therefore detectable. These pipes are defective.
Fault image: asymmetric penetration due to a misaligned coil feed.
CrNi - tube 20*3 mm
Optical not visible, here the thermo profile is becoming more and more asymmetric, because of wear and tear or insufficient lubrication on a roller set.
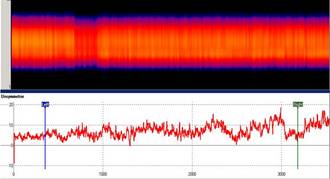
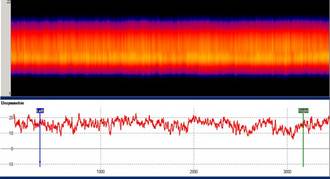
Task
- Monitoring and presentation of the penetration while production of an afterwards calibrated and completely closed welding wire.
- Reference: plant manufacturer Bühler Würz Kaltwalztechnik GmbH, Pforzheim
- tube: 12* 2mm filled with pouder welding speed: 15 m/min
The WeldQAS-System calculates for each profile (200 times per sec) characteristics of the thermal field which find use as monitoring values.
It is able to measure other parametres of the machine, e.g. laser power and speed beside the temperature field, take them up synchronically and to monitore at the same time.
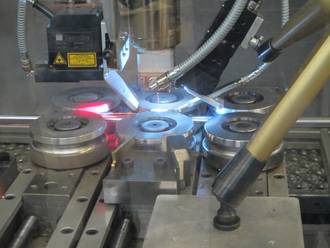
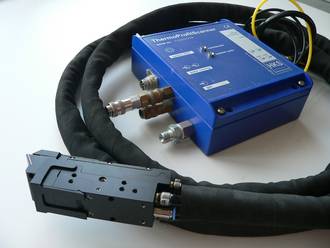
Application data TPS
- water cooling integrated
- anti-spatter protection
- mechanical self-protection shutter
- temperature control of the record electronic
Penetration control
example:
Laser absorption as wished - penetration consistant and up to 90 % of the seam.
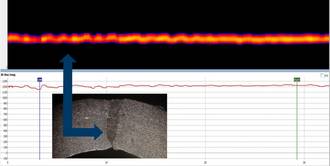
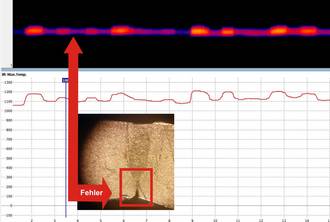
Penetration control in case of divergences of the laser power
example:
constant, but too low penetration, less than 80%
Penetration control in case of divergences of the laser position
example:
even divergences of the laser of 0.05 mm over the zero bondline are clearly visible as asymmetric penetration
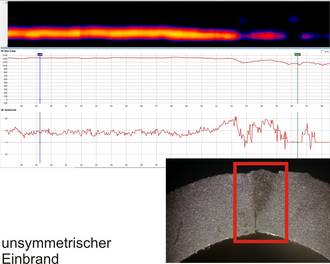
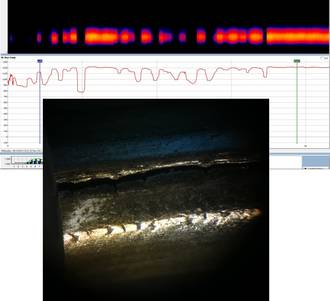
control of the fusion penetration if there is an open gap
example:
If there is a small gap in the welding groove the laser cannot insert his energy.
The fusion penetration is not enough.
Task
- Recognition of visible and invisible welding inconsistenciesas holes, pores larger than 1 mm, edge fusion faults and penetration fluctuations.
- Recognition of “weldability” problems with supplied materials.
- The existing eddy current detection system does not fulfill requirements.
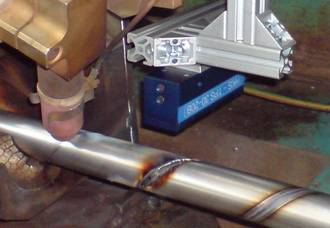
ThermoProfilScanner
offset to the torch: 40 mm
scan frequency:100 Hz
resolution: 0,9 mm
working distance:20-60 mm
purging gas: 3 l/min
welding speed up to 3,5 m/min
water cooling via power source
Work monitor with actual seam evaluation and heat signature
Captured are:
- Welding current,
- Voltage,
- Shield gas amount,
- Band position and -speed
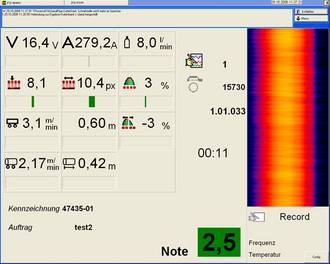

Heat signature of a 6 m tube
Fault image: Burn trough
CrNi – Band 73*1,0 tube 32mm
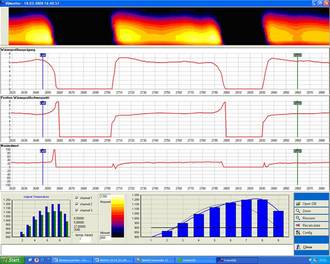
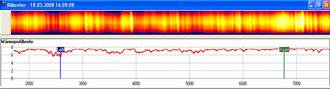
Fault image: Uneven heat distribution
Steel band 86*1,5 – tube 38 mm
Uneven heat input and penetration fluctuations due to defective band material (Seam appearance – fish scaling)
Fault image: Seam offset / seam position
CrNi - Band 73*1,0 tube 32mm
Such seam offsets causing welding seam to fail when the tube is pressurized.
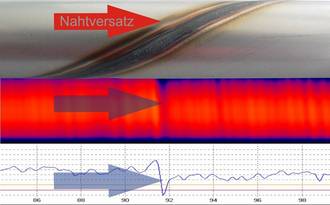