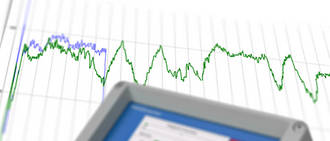
The complete and continuous documentation of welding processes in the production department is advantageous from the competitive point of view. The importance of queries as regards the product liability as well as tracking the production processes through quality assurance is ever increasing.
In addition to the knowledge about process parameters, (welding current, voltage, wire feed, gas volume, temperature, etc.), information regarding the load as well as wire, gas and power consumption is requested for calculative evaluations.
HKS offers production documentation in 3 areas of applications:
- Documentation of a workstation equipped with portable WeldScanner
- Documentation of complete assembly lines containing several welding devices with WeldAssist
- Monitoring the automated welding processeswith WeldQAS.
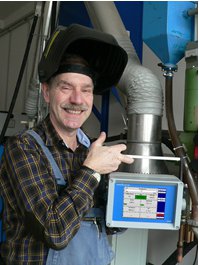
In the welding technology training program, the accurate knowledge of process parameters helps in understanding the correlation between device settings and welding results.
Changes in operating points or the effect of different shielding gases can be explained using measuring technology.
Thanks to the option of a direct connection for large displays or projectors, WeldScanner is especially suitable for theoretical and practical training.
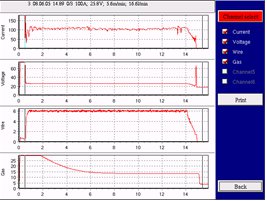
The value set for the power sources must correspond to the displayed variables to ensure adherence to the standard and specifications when welding. The calibration mode of WeldScanner can easily be used for this purpose.
In combination with a load resistance that simulates arc welding, the actual value of process variables can be compared with the set value. Calibrated sensors are used to prepare a calibration log to ensure that the set variables match the process variables.
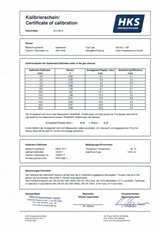
The temperature cycles observed during the welding process have a decisive effect on the mechanical properties of the welded product and on the thermal influence zone. The cooling time has proven to be a good indicator for evaluating the effect of cooling speed on material properties. It is the time required for cooling a welding seam and its thermal influence to pass through a temperature range of, e.g. 800 °C to 500 °C (T85-time).
In combination with a temperature sensor (pyrometer or thermo couple), WeldScanner can calculate and display the cooling time immediately after a measurement.
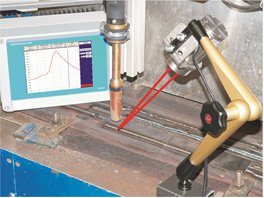
Irregularities and deviations from quality standards can be represented through a high-resolution recording of current and voltage.
For example, the following can be identified:
- Defective power sources
- The effect of wire speed and gas volume on the result
The correlation between the contact pipe wear and the changes in process variables. This “detailed” overview of process variables in the welding process naturally helps in optimising the systems.
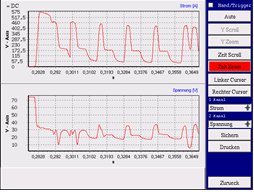