is used for automatic quality monitoring and documentation in industrial production for welding methods such as:
- Gas-shielded metal arc welding
- Resistance welding
- Stud welding
- Laser welding
- High-frequency welding (conduction and induction welding)
- Clinching
Automated welding processes require automated quality checks.
The WeldQAS system is an automatic welding process monitor and controls 100% of the production.
Since parameters are directly monitored during the welding process, an immediate reaction is possible in case of an error thus averting consequential damage.
WeldQAS can be used to acquire latest knowledge about welding production, to optimise it and use it cost-effectively in the production processes.
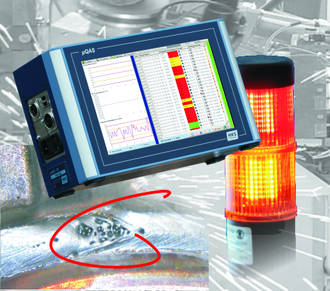
It records welding parameters during the welding process (online) without fixing any attachments on the torch head.
It is based on a new technology of recording high-resolution digital data and intelligent process data processing in a signal processor.
Using patented algorithms and welding parameters, it allows detection of pores, burn-through, wire defects (MSG) and other welding irregularities.
With the help of the patented ThermoProfilscanner
,WeldQAS also monitors the thermal field of the welding seam that is solidifying and uses this as a quality feature.
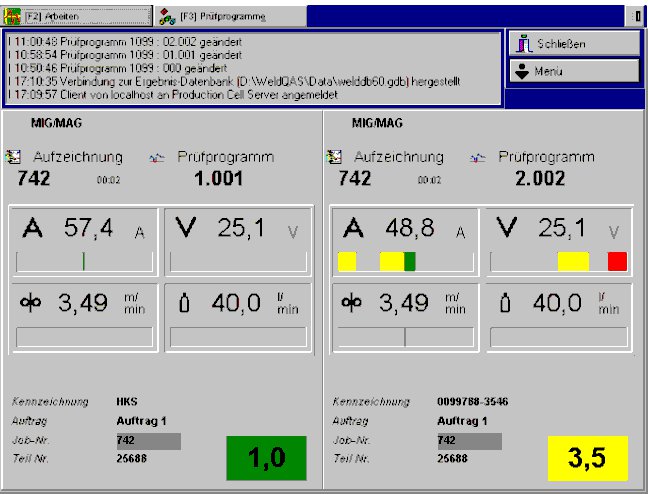
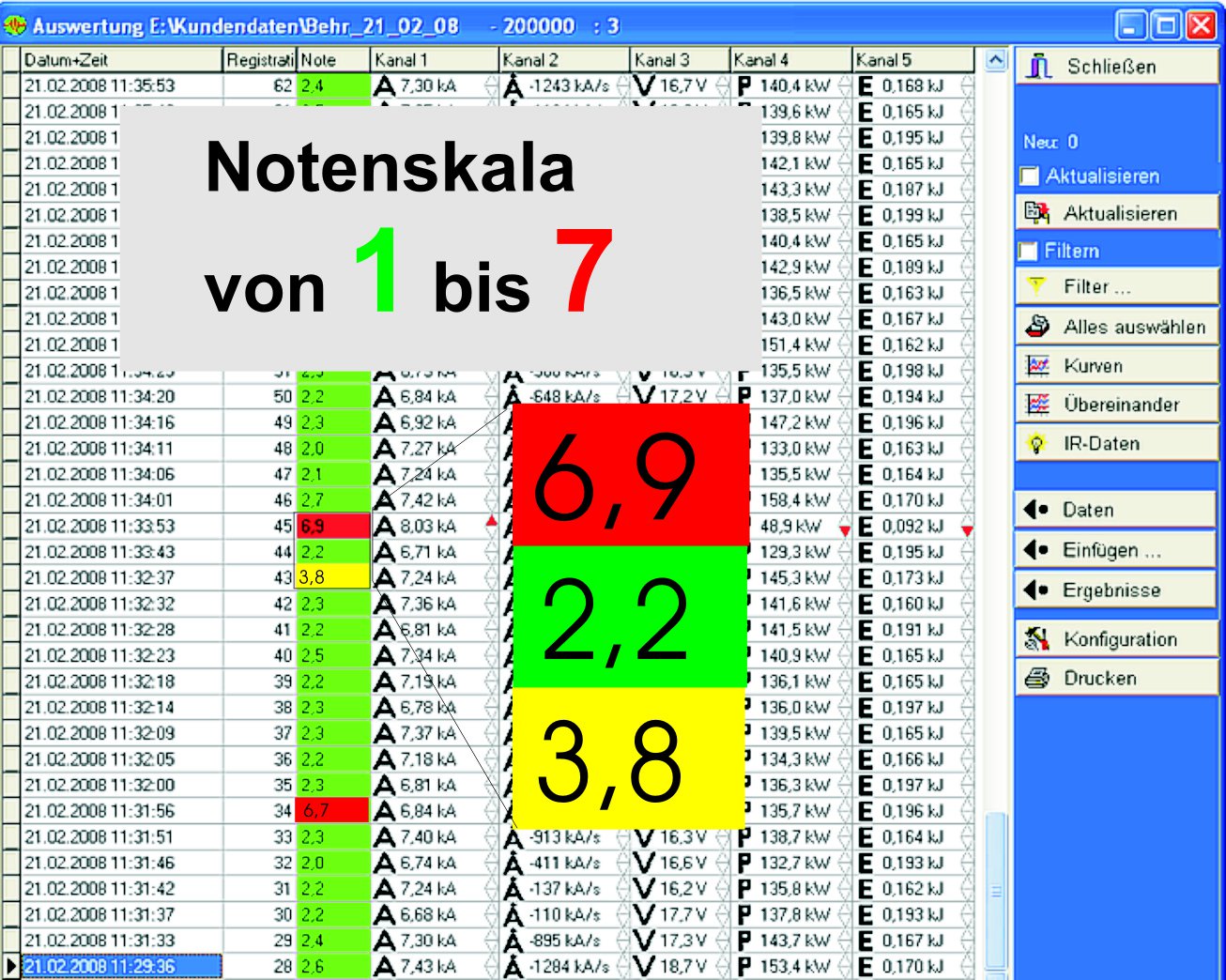
WeldQAS records the data in databases and provides an overview for optimising and stabilising the welding production. It is network compatible and the data is automatically stored on a central server.
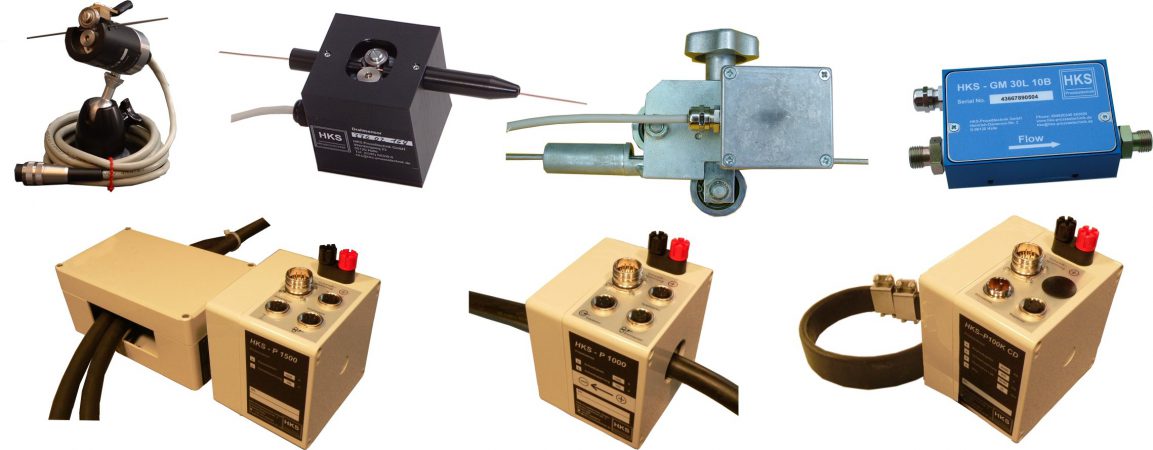
The series comprises basic devices WeldQAS-S3 as compact- or power version (cabinet, console), to which sensors (see the figure) can be connected for recording the process variables.
Process variables can also be recorded using industrial fieldbus systems or power source-specific buses.
Reduced production costs due to the highest possible reliability throughout the production process
Avoidance of rework and expensive product recall
- ecognizing changes in the welding parameters quickly
- prevents further production of faulty parts in quantities
- 100% checkup of all welded seams according to the same criteria
- optimization of the welding processes by means of trend analyses and evaluation tools
- WeldQAS “forces” reproducible evaluation of the welding parameters
Upgrading at the audit
- WeldQAS ist an accredited welding monitoring system and fulfils all requirements of external auditing
- complete traceability by means of result reports
Investment has a lasting effect with a short return flow
- one system for all welding methods and welding machines (one time effort for training)
- considerably lower investment costs in comparison with visual systems for weld inspection
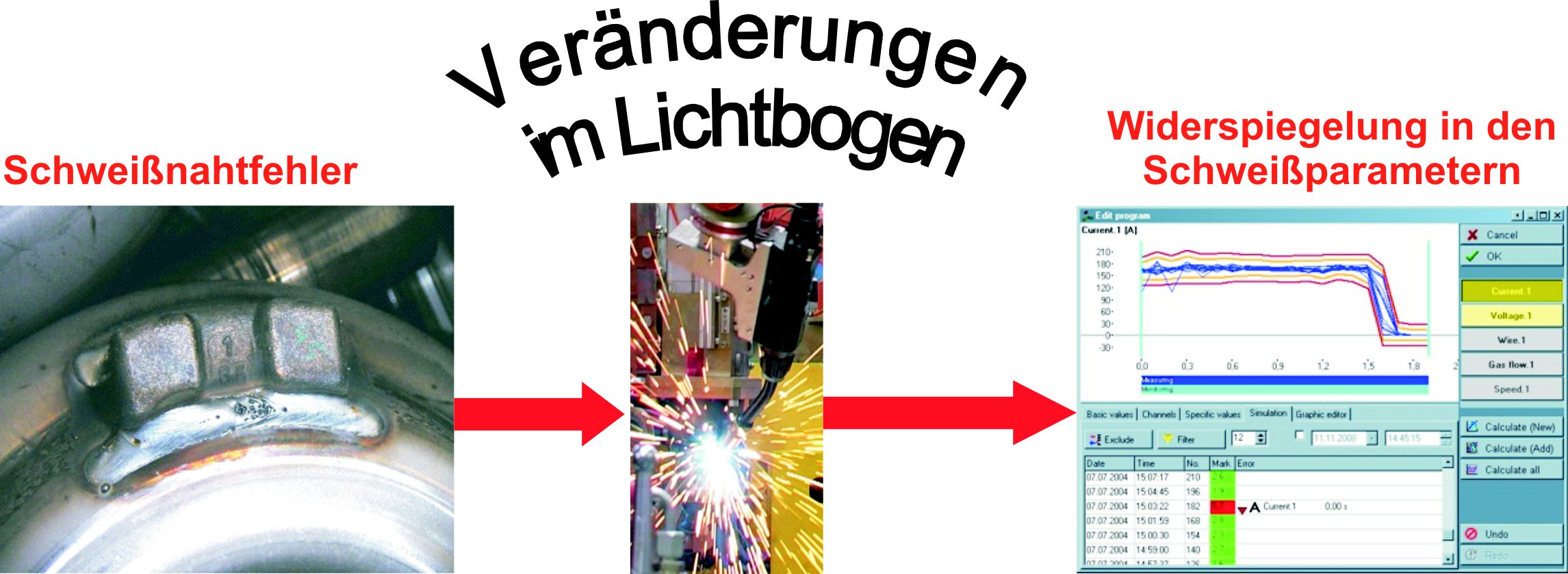
Basis
Weld faults lead to changes in the arc which are reflected in the welding parameters
Impact of the ASP technology
- Measurement of the welding parameters with 50 kHz (every 0,00002 second)
- Compression of the values by means of signal processor to process characteristics with intelligent algorithms
- Comparison with reference curves during welding
- Inquiry of divergent vectors as a quality mark
- immediate visualisation and output of defects with bad quality marks
- All parameter courses and supervision results are recorded and put into the archives.
The WeldQAS in the new generation S3 is available in 2 versions:
- compact - version
standard device for the monitoring of one or two welding torches
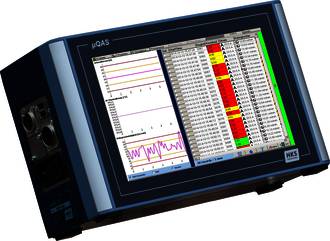
- dimensions: 330*200*135mm (stand-alone or wall fastening)
- multi-touch-display 10.1 inch
- highest reliability by passive cooling and industry flash memory
- Ethernet, USB, HDMI or VGA (optional)
- closed operating system Windows embedded, WeldQAS software
- direct connection of the sensors ( 8 differential inputs with 25 kHz or 4*250 kHz, 3 counter inputs 100 kHz, TPS)
- 24 separate in- and outputs
- Profibus/Profinet integrable
- cabinet - version
as cabinet or console - version for complex sites with more than two welding torches, multiple head SAW insatllations, endless tubbe production...;
consiting of a display and measuring unit
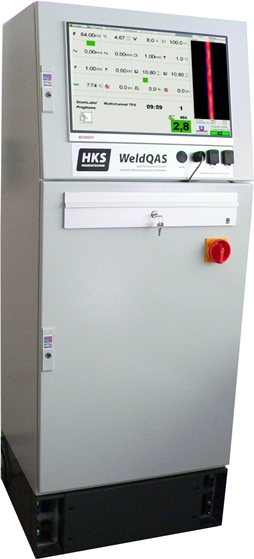
(as control cabinet or console)
- System for complex sites with more than two welding torches,
multiple head SAW installations, endless tube production…, - consisting of a display and a measuring unit
Display unit:
- integrated in control cabinet or separable
- powerful passive cooled CPU with touch-display
- separable from the measuring unit up to 200m via HKS-ethernet
- industry flash memory with closed Windows embedded
- unlimited amount of measuring channels
- database server integrated.
Measuring unit:
- version available as control cabinet or console
- channel number configured by multiple measuring modules
- integration of additional modules for galvanic isolation, additional relay, central power supply 24 V
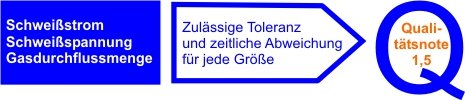
Evaluation through a quality rating
In a stable and quality-compliant welding production, the measurable parameters (welding current, welding voltage) vary in stable patterns. Deviating changes indicate problems.
The evaluation model of WeldQAS analyses these deviations with a rating between 1 and 7 that is proportional to the magnitude and the time duration of the deviation. In case of a good rating, all variables are within the permissible tolerances.
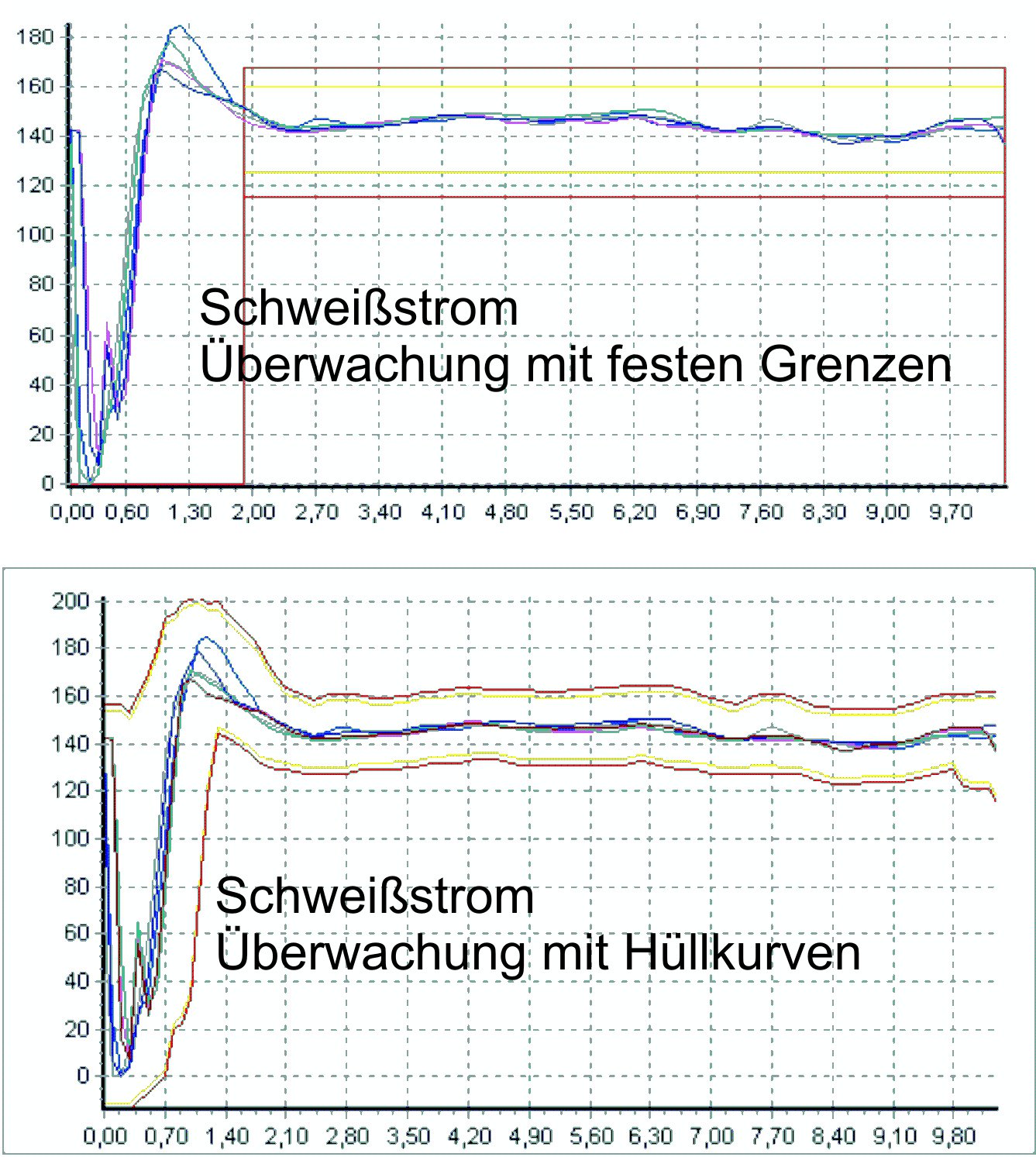
Monitoring using envelope curves
Unlike the monitoring using fixed limits (for processes that can be defined chronologically - masking of start and end times), monitoring using envelope curves allows up to 40% better detection of welding faults due to:
- Monitoring of all sections of the welding process
(including ignition and crater fillings) - Precise adaptation of monitoring as per the “natural” progression of welding process parameters
- Especially suitable for fully automated welding processes
(robot welding)
The WeldQAS system supports the tolerance specifications with fixed limits (e.g. for extremely long welding seams or in the UP area) as well as monitoring using envelope curves.
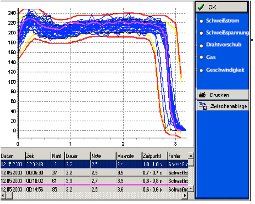
Automatic statistical learning process
The WeldQAS system is an unique system that offers an automatic learning function from the recorded data parallel to the ongoing production.
The signal behaviour is statistically analysed and abnormal sequences are automatically ruled out.
Figure: Monitoring limits (errors) have been automatically learnt from the progression of several welding processes shown here.
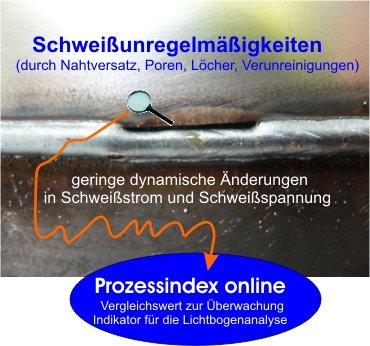
Pioneering Fault Detection (PFD)
Patented fault detection by evaluating the electric arc dynamics
The PFD process is based on determining a process index and
detects minor dynamic changes in the welding current and welding voltage in case of welding irregularities such as
- Pores, holes, contaminations
- Seam offset, incomplete fusion, weld penetration faults
- due to the effect of gas and wire
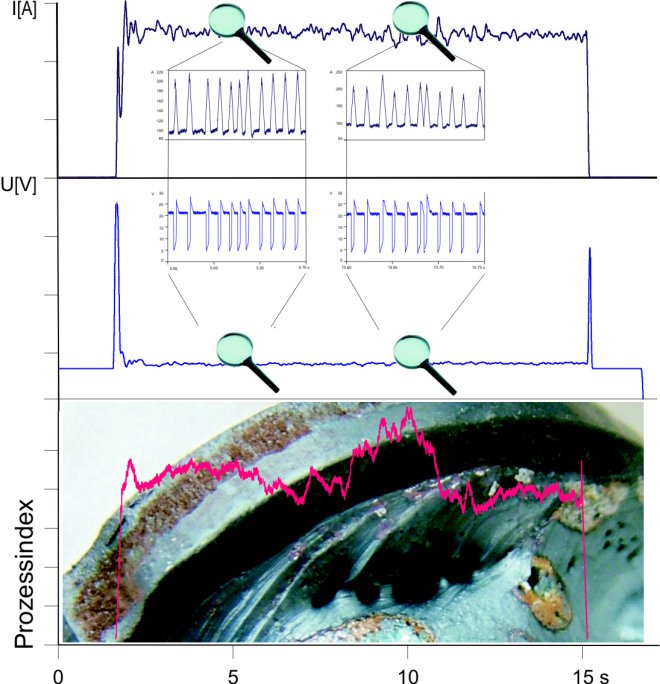
The process index
- is calculated online only from highly dynamic progressions of current and voltage
- is independent of the welding current to a large current
- does not require any learnable pattern
This results in
- a comparison value for monitoring the automated production
- an indicator for electric arc analysis
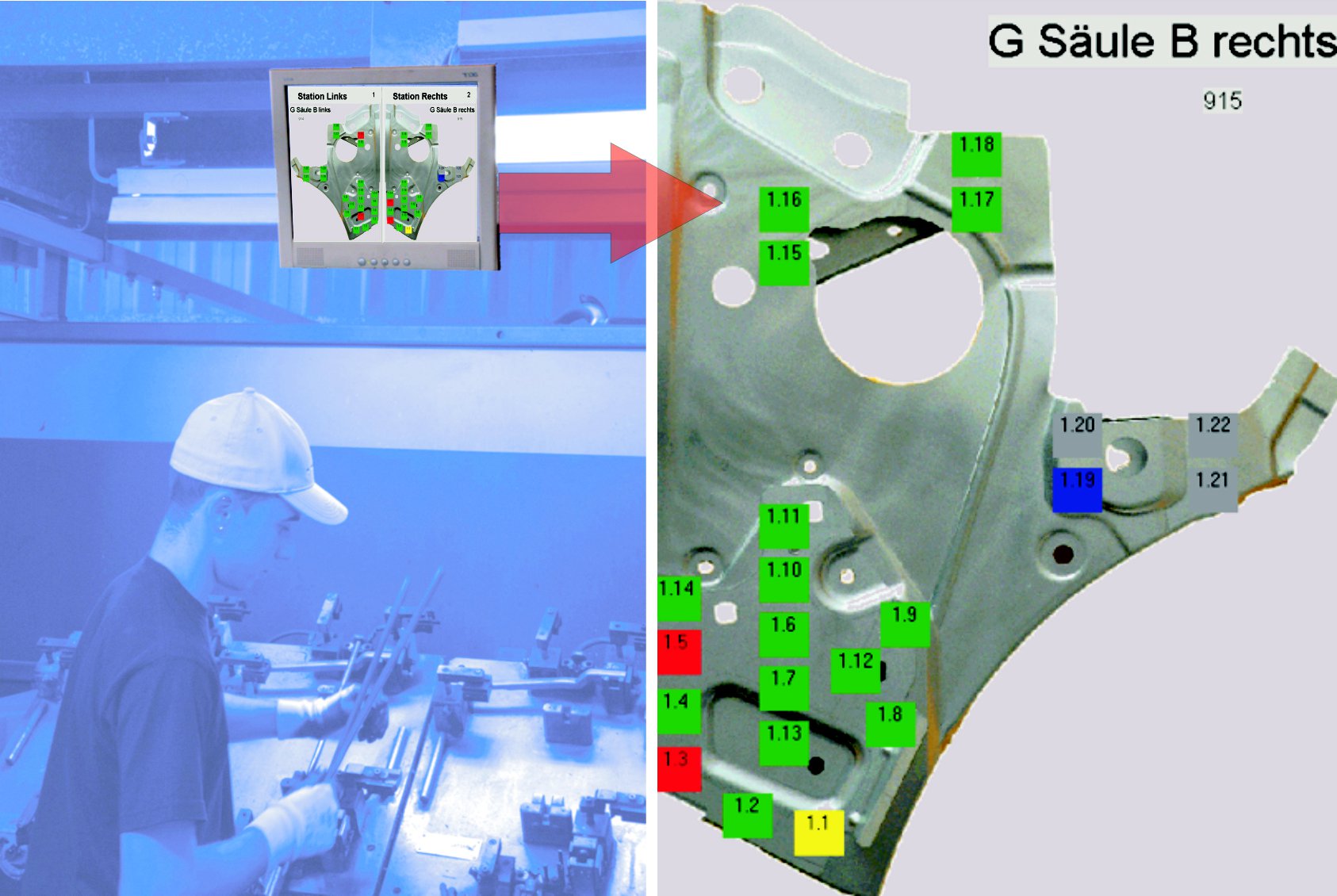