A new system for nondestructive testing on base passive thermography gives many advantages in quality control in tube production lines.
Possible is that by a special designed thermo line camera (sensor), not based on the standard optical technology. With this special for welding application designed sensor, is it possible to measure the temperature on a line cross the seam. Many such profiles added together shown a thermo image from the seam. Every one temperature profiles shows welding imperfections as unsymmetrical penetration, not enough penetration depth and many kinds of other imperfections (holes, pores,..)
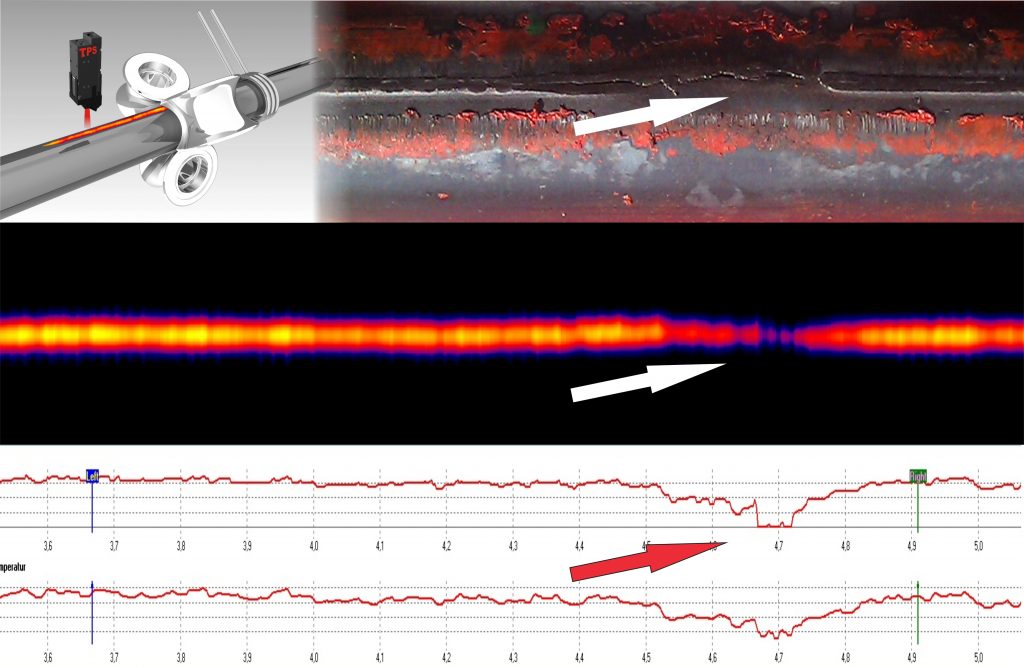
Based on real thermo images in TIG-welding tube lines and ERW (HFI) tube mills will be shown the excellent advantages compared to eddy current testing and ultrasonic inspection in such kind of seam control.
With this method will be indicate “cold” seams in HFI-welding tube mills and not middle position of the tungsten electrode in TIG welding applications.
The all-time shown real thermo field on a monitor gives the welder on the tube mill a real “look in to the seam” during the running machine.
Visit us at the world’s most important trade fair for the pipe industry
in Hal 6 D15